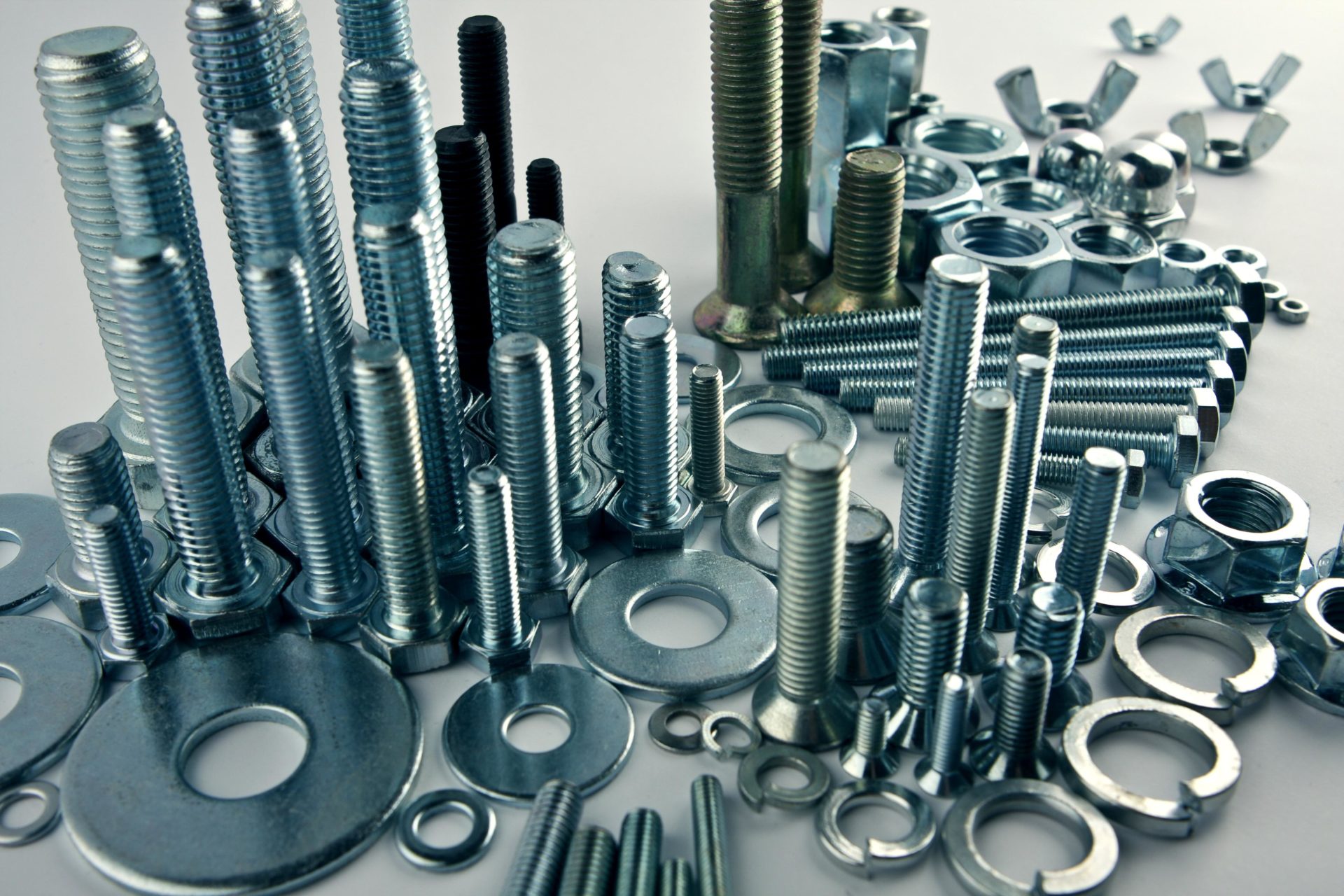
July 6, 2021
Updated on September 13th, 2021
The video of the webinar is now available either in our Webinar archives or on our YouTube channel. Follow the links below to watch the webinar, and feel free to reach out to us should you have any question or comment.
Want to know what simulation can tell you about your die progression design? This webinar goes through all the tools available to users.
Simulation by Transvalor is the accurate and easy software to quickly understand how a piece of metal is deformed during forging. The software provides the springback of the part after each forming station to accurately design the full die progression, and have it right the first time in production.
Learn how to save a tremendous amount of money by predicting your actual forming process.
The webinar goes through the specific benefits of using simulation for fasteners manufacturing. Tools such as grain flows, points tracking, multi-views, and many more are crucial to accurately assess the quality of the progression design. We will discuss the tools available to users to detect defects, and understand how defects happen during the progression and make proper adjustments to get rid of them.
During the session, we will present an example of screw deformation progression from wire to finished part. We will go through a bolt forming process as well. We will touch on the importance of proper pre-stressed die in increasing your die life and avoid breakage with a full forging die analysis.
While Transvalor offers several software able to simulate cold forging processes of steel and other materials, COLDFORM® comes with an optimization module. The automatic optimization not only has the ability to run a Design Of Experiments (DOE) to compare multiple trials users have in mind, the optimization goes deeper in providing automatically the best set of parameters to reach the users end goal. We will present an example applied to a screw to optimize in-use properties. This is a crucial tool to help decide what version is best for the use of the part.
Finally, while several joining processes exist, such as welding, brazing, adhesive bonding, we will focus on mechanical joining processes, which can be simulated with our simulation software COLDFORM®. Mechanical joining is a process for joining parts through mechanical methods, which often involve threaded holes. Joining parts using screws or nuts and bolts are common examples of mechanical joining. The threaded holes employed for mechanical joining are vulnerable to fractures. In ductile materials, the fracture can come from fatigue, while in brittle materials, the fracture can simply result from mechanical overloading. Thus, mechanical joints must be designed with fatigue failure and brittle fracture in mind. The simulation of these processes enables users to predict such phenomena. Designers can then revise their design to decrease the risk of die failure or part in-use failures.
This “How to simulate a die progression for fasteners” webinar offers a great understanding of how simulation plays a crucial role in the design process. It is a time saving and money saving tool that greatly benefit any company size. Transvalor Americas offers a wide range of opportunities to access simulation either through simulation service, lease, or purchase solutions. We are dedicated to help our customers getting the most out of our solutions in the most efficient and economical way.
Watch this webinar right now through our Webinar Archives.
Transvalor Americas Team